Production
Making of the 400 E lamps. Production facilities were rather simple, a shack on the country side.
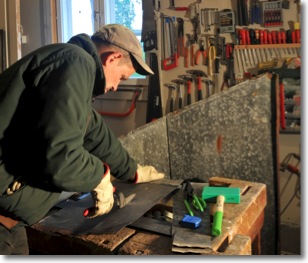
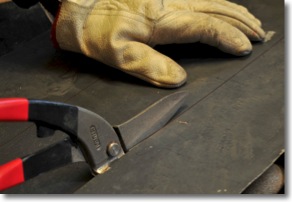
The “factory” where the lamps were produced. A total of 135 lamps were made, a job that took some 3 weeks all together.
Stubai Cutting scissors for sheet metal, most likely the best scissors in the market. Here old roof plate is being cut. There is still a long way to go before the lamp is ready.
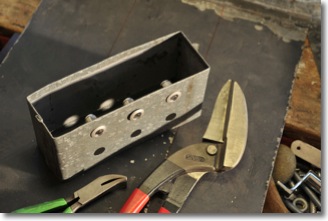
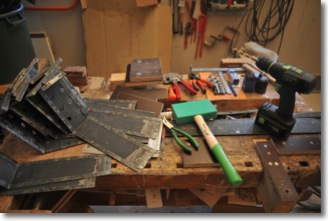
One of the very first prototypes to be made. The body is made out of one swept part with one squeezed seam. The making of the body took more time than expected, since it included far more steps than first intended. Bending both long sides, drilling of the light holes (first 6 mm holes and then the 15 mm holes) + the holes for the plywood side parts (16 holes) and the electrical cord. Some 29 holes in the main body, +2 in the plywood +3 holes in the shaft had to be drilled so a total of 34 holes had to be drilled in each lamp.
To the right, at left the swept parts with holes, some 3 bends later the metallic body was ready and the electrification and final stage, 16 small screws , of assembly was to be done and the lamp was ready. Hand tools needed for the “production”, they are all normal roofing tools, scissors, pliers, soft plastic hammer and talmeter measuring tape.
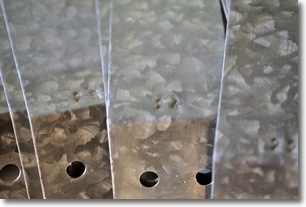
All lamps carry a unique number, stamped on the backside of it. The numbers stamped on every single plate / lamp makes it possible to identify from which roof the plate originates.
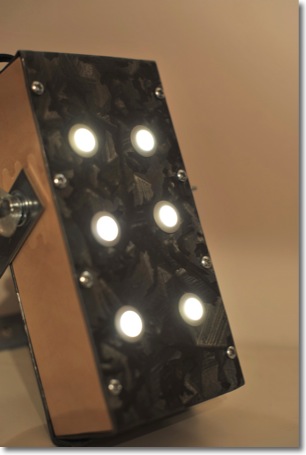
The final product a 400 E ready to be delivered. The frame is attached to the body with wing nuts..